Understanding Precision Injection Molded Plastics
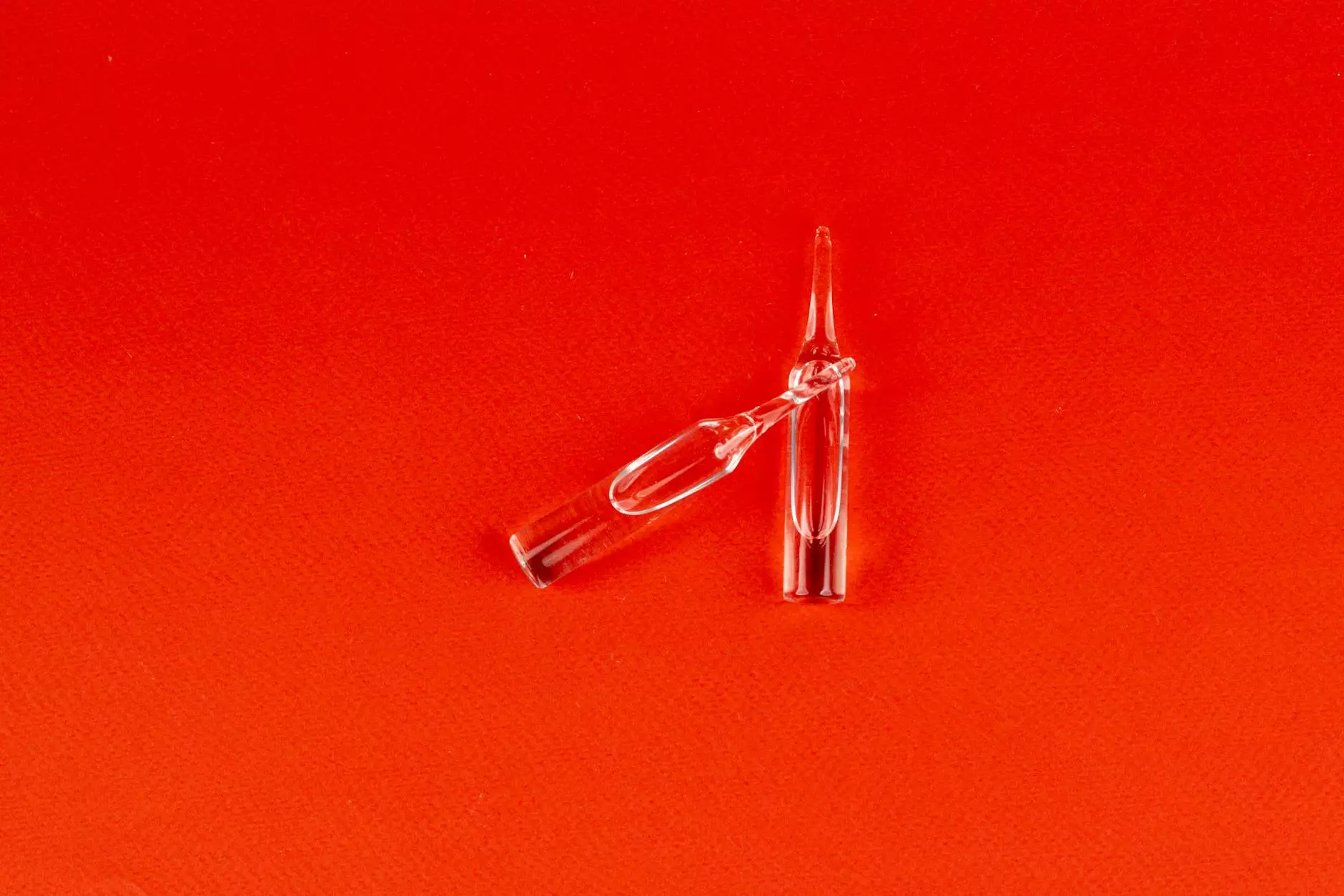
Precision injection molded plastics play a crucial role in today's manufacturing landscape, especially within the realm of metal fabrication. As industries continually demand better performance and higher adaptability, the integration of precision plastic components has emerged as a pivotal solution that enhances productivity and efficiency.
The Mechanism Behind Precision Injection Molding
At the core of precision injection molded plastics lies the injection molding process, a manufacturing technique used to produce parts by injecting molten material into a mold. This method is not just restricted to metals; it has found significant applications in plastics, thereby revolutionizing how products are made.
How Injection Molding Works
- Material Selection: The process begins with selecting the right plastic materials—typically thermoplastics or thermosets.
- Melting the Plastic: The chosen material is heated until it reaches a molten state.
- Injection into Mold: The molten plastic is injected under pressure into a specially designed mold.
- Cooling and Solidification: Once injected, the plastic cools and solidifies, taking the shape of the mold.
- Part Ejection: Finally, the newly formed part is ejected from the mold and subjected to finishing processes.
Advantages of Precision Injection Molded Plastics
The advantages of utilizing precision injection molded plastics are numerous and far-reaching. These benefits significantly contribute to the efficiency and versatility of metal fabrication as an industry.
Cost-Effectiveness
One of the most compelling reasons to choose precision injection molding over traditional manufacturing methods is its cost-effectiveness. The ability to produce complex parts in large volumes reduces the unit cost, making it an attractive option for manufacturers.
High Precision and Detail
Another notable advantage is the high level of precision achievable. Modern injection molding technologies allow for intricate designs with tight tolerances, which is essential in sectors like automotive and aerospace, where even minute deviations can have serious repercussions.
Material Versatility
Precision injection molding can accommodate a variety of plastic materials, including ABS, polycarbonate, and Nylon, enabling manufacturers to tailor their products based on physical and chemical properties required for different applications.
Reduction of Waste
The injection molding process is highly efficient, generating minimal waste compared to other manufacturing processes. Combined with the capability to recycle scrap material, this attributes to a more sustainable manufacturing practice.
Applications of Precision Injection Molded Plastics in Metal Fabrication
The incorporation of precision injection molded plastics in metal fabrication is not merely a complementary addition; it is a transformative force that is reshaping the production landscape. Below are some of the main applications of precision molded plastics:
1. Automotive Industry
- Interior Components: From dashboards to door handles, precision-molded plastics create critical components that are both lightweight and durable.
- Exterior Elements: Bumpers and trims made from injection molded plastics provide aesthetic appeal alongside functionality.
2. Electronics
- Enclosures: Precision molded plastics offer electrical insulation and protection for sensitive electronic components.
- Connectors: The manufacturing of connectors for cables and circuit boards heavily relies on the precision molding process.
3. Medical Devices
- Single-Use Devices: Many medical devices require stringent hygiene standards, which precision molding can meet through the use of sterilizable plastics.
- Complex Assemblies: Devices featuring intricate designs for better functionality are increasingly being made using this technique.
4. Consumer Products
- Household Goods: Many everyday items, from kitchenware to toys, benefit from the durability and design flexibility offered by precision injection molding.
- Packaging Solutions: Packaging for food and consumer goods made from molded plastics provides both protection and convenience.
Challenges in Precision Injection Molding
While there are numerous benefits to using precision injection molded plastics, it is essential to also consider the challenges that manufacturers may face in this domain.
High Initial Investment
The setup costs for precision injection molding can be significant, due to the need for custom mold designs and production equipment. This can be a barrier for small businesses entering the market.
Quality Control
Ensuring consistent quality across high-volume production runs can pose challenges, requiring stringent quality control measures throughout the manufacturing process.
Material Limitations
While there is a vast range of materials available for injection molding, not all plastics are suitable for every application. Selection must align with the desired properties of the final product, which may require extensive testing.
Future Trends in Precision Injection Molded Plastics
The future of precision injection molded plastics is poised for remarkable growth as advancements in technology continue to provide enhanced capabilities and reduced costs. Here are some trends to watch:
1. Automation and Industry 4.0
With the rise of smart manufacturing, integration of automation into the injection molding process is becoming increasingly prevalent. Automation can improve efficiency, reduce labor costs, and enhance production consistency.
2. Sustainability Initiatives
As industries move toward more sustainable practices, the focus on recycling plastics and utilizing biodegradable materials in injection molding is on the rise. This trend aligns with global environmental goals and consumer demand.
3. Advanced Materials
Innovations in material science may lead to the development of stronger, lighter, and more adaptable plastic composites. These advanced materials could open doors to new applications in sectors previously dominated by metals.
4. Customization and Personalization
With the growth of customization in consumer products, precision injection molding is becoming an essential mechanism for producing tailored solutions that meet individual customer needs.
Conclusion
In summary, precision injection molded plastics are revolutionizing the metal fabrication landscape by providing solutions that increase efficiency, enhance design flexibility, and reduce costs. As we continue to see advancements in technology and a shift toward sustainability, this area of manufacturing is likely to play an even more critical role in various industries.
Companies, like those in the deepmould.net, are at the forefront of this transformative movement, harnessing the power of precision injection molding to deliver quality products that meet the diverse needs of their clients. As we move forward, the intersection of plastics and metal fabrication will undoubtedly yield innovative solutions and open new avenues for growth.