Unveiling the Innovations of an Injection Factory
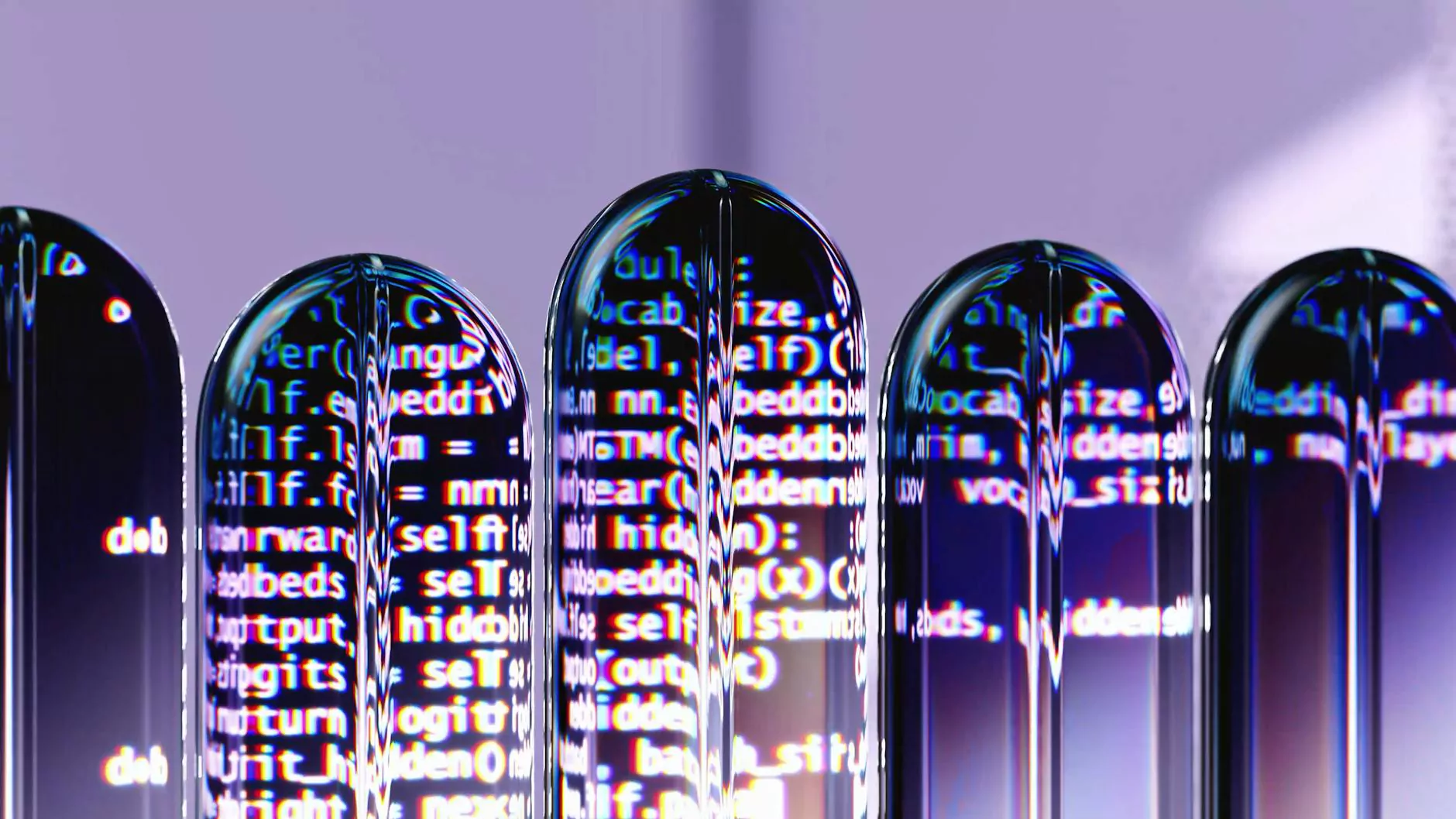
In today's fast-evolving technological landscape, businesses are continually searching for efficient and effective manufacturing processes. One such process that has gained immense traction is found in an injection factory. This specialized facility is crucial in the production of countless items, particularly those used in the domains of art supplies, product design, and 3D printing. Let’s dive deep into what an injection factory is, how it operates, and its significance in the modern business environment.
What is an Injection Factory?
At its core, an injection factory is a manufacturing plant that uses the injection molding process to create plastic products. This process involves injecting molten material into a mold to create items of various shapes and sizes. The versatility of injection molding makes it indispensable across several industries. From household products to intricate components in electronics, the applications are vast.
The Injection Molding Process Explained
The injection molding process can be broken down into several key stages:
- Material Selection: Different plastics are used depending on the desired characteristics of the final product. Common materials include ABS, polypropylene, and polycarbonate.
- Melting: The selected plastic is heated until it melts and becomes viscous enough for injection.
- Injection: The molten plastic is injected into a pre-made mold under high pressure.
- Cooling: After the mold is filled, the plastic cools and solidifies while still in the mold.
- Demolding: Once cooled, the mold opens, and the finished product is ejected.
This cycle is repeated many times, allowing for mass production of identical items at a very efficient rate.
Benefits of Using an Injection Factory
Utilizing an injection factory offers businesses numerous advantages:
- Cost Efficiency: Injection molding allows for high-volume production, which lowers the cost per unit as volumes increase.
- Design Flexibility: Products can be designed with intricate details and complex geometries, which are often challenging to achieve with other methods.
- Durability: The final products tend to be strong and reliable, which is crucial in sectors like art supplies where durability matters.
- Speed: The rapid production cycle means businesses can bring products to market faster.
- Waste Reduction: Injection molding minimizes waste by using materials efficiently compared to traditional crafting methods.
The Impact of Injection Factories in Art Supplies
In the realm of art supplies, injection factories play a pivotal role. Products such as paint bottles, brushes, and even sculpting tools often rely on the precision and efficiency of injection molding. The ability to produce large quantities of these items rapidly leads to:
- Standardization: Consistent quality across all products ensures that artists can rely on the tools they use.
- Innovative Materials: New types of environmentally friendly plastics can be utilized, supporting eco-conscious artists and suppliers.
- Custom Shapes and Designs: Artists often seek unique tools; injection molding allows producers to create bespoke solutions tailored to specific artistic needs.
Product Design and the Role of Injection Factories
Modern product design often hinges on the capabilities of injection factories. The integration of computer-aided design (CAD) software has transformed how designers envision products. Here's how an injection factory enhances product design:
- Rapid Prototyping: Designers can create prototypes quickly, testing different shapes and functionalities before full-scale production.
- Feedback Loop: The speed of production also accelerates feedback from users, allowing for design adjustments early in the process.
- Scalability: Designers can scale successful prototypes into mass production without losing quality.
3D Printing and Injection Factories: A Complementary Relationship
With the rise of 3D printing, many wonder about the relationship between these technologies and injection factories. Surprisingly, they can complement each other significantly:
- Prototyping: 3D printing is often used for making initial prototypes that can be tested before committing to the injection molding production process.
- Complexity: While injection molding is suited for mass production, 3D printing is ideal for producing intricate, one-off designs that may not be cost-effective to mold.
- Material Exploration: Both technologies allow for experimentation with new materials, which can lead to innovations in product design.
Challenges Faced by Injection Factories
Despite numerous benefits, injection factories also encounter challenges that businesses must navigate:
- Initial Setup Costs: The costs to set up an injection molding operation can be high, requiring significant capital investment.
- Mold Maintenance: Molds wear over time and need regular maintenance or replacement, which can disrupt production schedules.
- Material Limitations: While there are many types of plastics, specific applications may require materials that are not suitable for injection molding.
Future Trends in Injection Factories
The future of injection factories looks promising, with several trends emerging:
- Sustainability: Increasing emphasis on using sustainable materials and processes to reduce environmental impact.
- Smart Manufacturing: The integration of IoT devices for real-time monitoring and automation will enhance efficiency and reduce downtime.
- Customization: Growing demand for customized products will lead to innovations in mold design and production techniques.
Conclusion: The Vital Role of Injection Factories in Business Growth
As we explore the landscape of modern manufacturing, it's clear that an injection factory is more than just a production facility; it serves as an engine of innovation and efficiency that drives the art supplies, product design, and 3D printing industries forward. The synergy between traditional manufacturing and advanced technologies heralds a new era of possibilities, making the expertise found within injection factories invaluable.
As businesses continue to evolve, leveraging the advantages offered by injection molding will be crucial for success in a competitive marketplace. Embrace these innovations, and position your business for future growth through strategic partnerships with quality injection factories.
For more insights into the transformative world of injection molding and its applications in art supplies, product design, and 3D printing, visit us at arti90.com.