Understanding the Role of Connecting Rod Manufacturers in Diesel Engine Performance
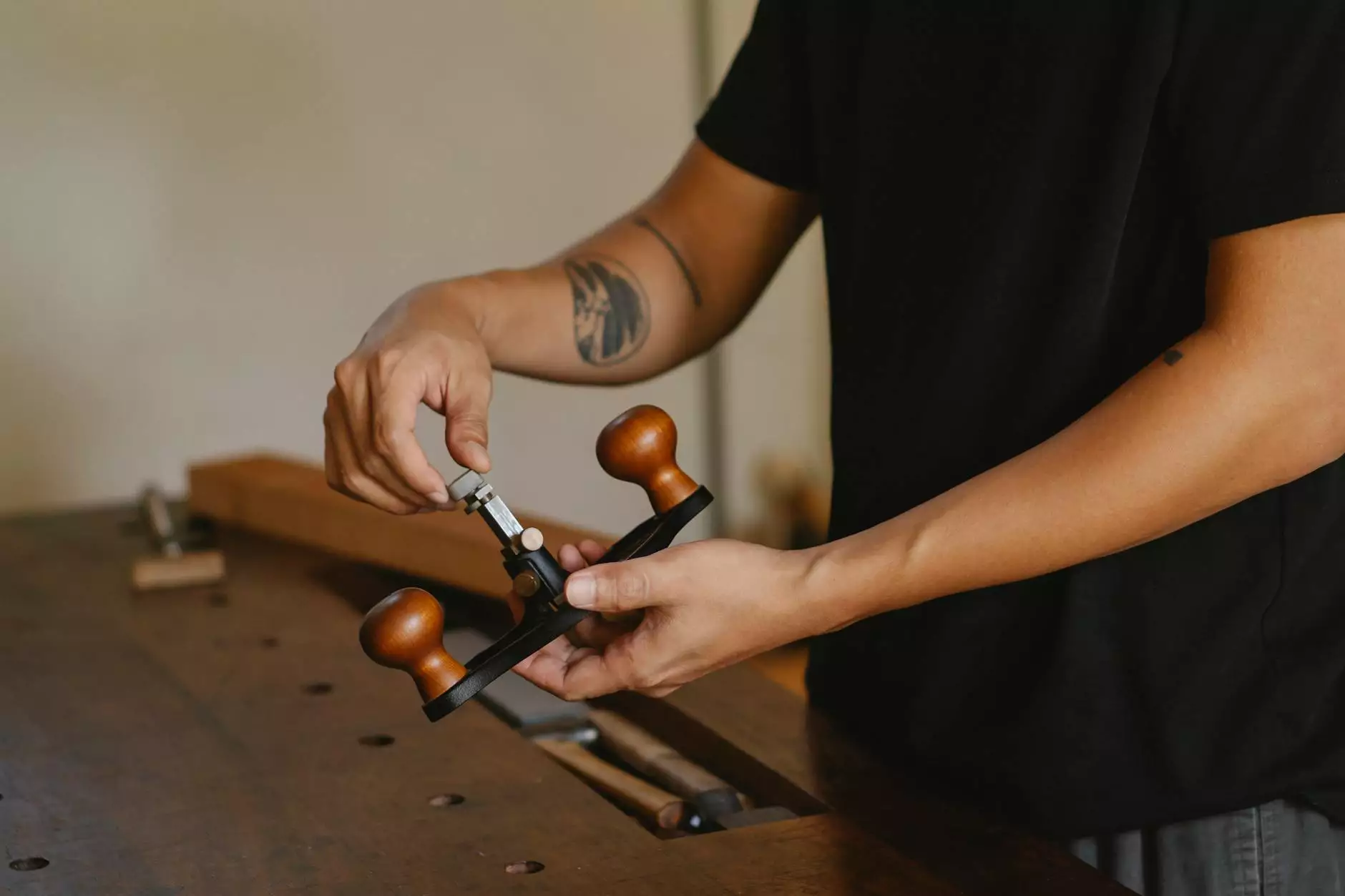
The connecting rod manufacturers play a pivotal role in the automotive and diesel engine industries. These components are crucial for ensuring that the engine runs smoothly, efficiently, and with optimal power output. In this article, we will delve deep into the world of connecting rod manufacturing, exploring the processes, materials used, and the importance of quality assurance in achieving the best engine performance.
The Importance of Connecting Rods in Diesel Engines
The connecting rod is a fundamental part of the internal combustion engine. Its primary function is to transfer the force generated by the combustion of fuel in the engine's cylinders to the crankshaft, converting it into rotational motion. This process is vital because:
- Efficiency: Connecting rods allow for efficient power transfer, contributing to the overall efficiency of the engine.
- Performance: High-quality connecting rods improve engine performance, enabling higher power output and better acceleration.
- Durability: Sturdy and well-manufactured connecting rods enhance the durability of the engine, reducing the risk of failure under stress.
- Vibration Reduction: Properly designed connecting rods minimize vibrations, leading to a smoother driving experience.
Materials Used by Connecting Rod Manufacturers
When discussing connecting rod manufacturers, it's essential to understand the materials used in their production. The choice of material is critical in determining the performance and longevity of the connecting rods. Common materials include:
- Steel:
Most connecting rods are made from high-strength steel. The strength and ductility of steel make it ideal for handling the stress and strain experienced during operation.
- Aluminum:
Some manufacturers opt for aluminum connecting rods due to their lightweight nature. While not as strong as steel, they can improve overall engine efficiency by reducing weight.
- Titanium:
For high-performance applications, titanium rods are sometimes used. They are incredibly strong and lightweight but tend to be more expensive than other materials.
The Manufacturing Process of Connecting Rods
The process of manufacturing connecting rods typically involves several key stages to ensure precision and quality. Here’s an overview of these stages:
1. Design and Engineering
The first step for connecting rod manufacturers is designing the connecting rod according to specific engine requirements. Engineers use CAD software to create detailed designs that consider strength, weight, and performance parameters.
2. Material Selection
Based on the design, manufacturers select the appropriate materials. The choice involves balancing strength, weight, cost, and the engine's operational characteristics.
3. Machining
Once materials are chosen, the machining process begins. This step involves cutting, grinding, and shaping the material to form the connecting rod configuration accurately. CNC (Computer Numerical Control) machines are commonly used to ensure precision.
4. Heat Treatment
Heat treatment is critical for enhancing the mechanical properties of the connecting rods. Through processes like annealing or quenching, manufacturers can improve hardness and tensile strength, which are essential for high-performance applications.
5. Quality Control
Quality assurance is an integral part of the process. Manufacturers conduct rigorous testing, including dimensional checks, material inspections, and stress tests to guarantee that every connecting rod meets industry standards.
Choosing the Right Connecting Rod Manufacturer
When selecting a connecting rod manufacturer, several factors should be considered to ensure you obtain a reliable and high-quality product:
- Experience:
Look for manufacturers with extensive experience in the industry. Established manufacturers are likely to have a better understanding of the requirements and challenges of producing high-quality connecting rods.
- Quality Standards:
Ensure that the manufacturer adheres to strict quality standards, such as ISO certifications. This adherence typically indicates a commitment to quality and reliability.
- Material Options:
A good manufacturer should offer a variety of material options to meet specific performance needs and budget constraints.
- Customization:
Every engine has unique requirements; hence, a manufacturer’s ability to customize their products can be a significant advantage.
- Customer Support:
Reliable customer support ensures that any questions or issues during the purchasing process can be addressed promptly.
Innovations in Connecting Rod Manufacturing
The field of connecting rod manufacturing has seen several innovations that enhance the performance and reliability of these components. Some notable advancements include:
1. Advanced Materials
As technology advances, manufacturers are developing new materials that offer better performance. Composite materials and advanced alloys are being explored to achieve a superior balance of weight and strength.
2. Additive Manufacturing
3D printing and additive manufacturing techniques are increasingly being applied in the production of connecting rods. This method allows for more complex geometries and can lead to weight reductions without compromising strength.
3. Real-Time Quality Monitoring
Integrating real-time monitoring systems during the production process helps in catching defects early on and ensures that only quality components reach the consumer.
Conclusion: The Future of Connecting Rod Manufacturers
The role of connecting rod manufacturers in the diesel engine and automotive sectors cannot be overstated. As the demand for high-performance engines increases, these manufacturers will continue to innovate and enhance their processes and materials. By understanding the importance of connecting rods, the manufacturing processes involved, and how to choose the right producer, businesses can ensure they are equipped with reliable and efficient products.
For those interested in sourcing quality diesel engine parts and connecting rods, visiting reputable suppliers like client-diesel.com can provide invaluable resources. It’s essential to partner with manufacturers that not only offer expertise but also a commitment to quality and performance.